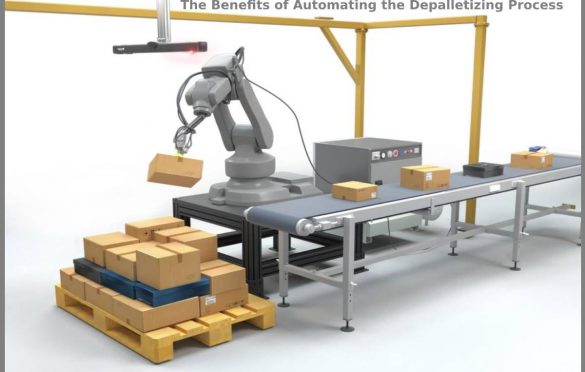
The Benefits of Automating the Depalletizing Process
The process of emptying boxes or bags from a pallet is referred to as depalletizing. Traditionally, it entails a demanding set of repetitive physical actions like heavy lifting, stretching, and bending. This physical effort might be hazardous if the cargo weighs more than 25 kg.
In reality, hand pickers are always under pressure to lift goods of various sizes, shapes, and masses. With the growth of e-commerce in 2020, the number and volume of Stock Keeping Units (SKU) being moved around on pallets has increased enormously.
Consequently, the demand for physical labor in warehouses has increased at an unprecedented rate. Furthermore, quarantine measures and social distancing created significant barriers. Because of these variables, automating the depalletizing procedure has become a real priority for high-volume logistics operations.
Traditional Depalletizing Procedures Have Limitations
Previously, robotic technologies could only choose products with identical characteristics. As a result, the pre-programmed system was unable to handle a wide variety of SKU variations. Human pickers, in general, are excellent at detecting and managing SKU variations, even on mixed-SKU pallets.
There’s no doubt that people are endowed with the cognitive capacity to identify the object, select them at their speed, and arrange it appropriately. Warehouse personnel must have job and safety education to work effectively.
Despite completing a planned training regimen, workers are still vulnerable to persistent physical problems. According to a survey, more than 36% of warehouse manual employees have shoulder and back injuries, resulting in missed working days due to handling and lifting heavy objects.
Human employees at risk cost organizations money in accident claims, safety education, and legal compliance expenses, all of which contribute to a higher turnover percentage. Furthermore, businesses must balance employing new employees with achieving stable or even improved throughput results.
Physical constraints, poor supervision, and bad ergonomics are some additional prevalent difficulties with manual handling. Consequently, there was a necessity to construct dependable robotic depalletizer systems that were devoid of human workers.
Automating the depalletizing procedure is no longer as difficult as it once was. Due to deep-learning algorithms, warehouses may now utilize a competent robotic depalletizing unit with a cutting-edge imaging system and a suitable gripper to carry the heaviest of products.
What to Consider When Automating the Depalletizing Procedure?
Essentially, human pickers do not make the best use of available warehouse space. Installing robotic depalletizer systems in warehouses allows for more effective use of the designated area, including the floor and the vertical space. Furthermore, this can improve overall performance by allowing manual employees to concentrate on more value-added jobs. If, for example, three out of six personnel conducted depalletizing procedures in addition to various other jobs, the depalletizing workstation would suffer.
On the other hand, a robotic depalletizer has 3D vision capabilities and a gripper that facilitates pick-and-place depalletizing activities. The 3D vision systems use vision software, multiple cameras, and laser sensors. The cutting-edge 3D visual system captures the surroundings and estimates the locations of randomly put objects.
It enables robots to detect each object, identify the pickup point, and put the object on a conveyor. After all, detecting unfamiliar objects at various heights is a straightforward step. With the sophisticated robotic depalletizer cell, it is even possible to recognize a package with DVDs as a single object rather than six individual boxes.
Finally, installing powerful vision software easily connects software and hardware components for a robot depalletizing unit. Vision software can increase item segmentation accuracy and allow robots to choose heavy things from a random pile.
Using Visual Technologies to Automate Depalletization
Robots can easily unload overlapping goods or shining things thanks to machine-learning algorithms and AI-driven vision technology.
This cutting-edge vision software enables an automated depalletizer to manage a continuous stream of mixed-SKU packages in any order. It can quickly identify the object on the pallet, detect variants, and manage them appropriately.
The advanced vision software segments classify, and recommend over 100 grip postures based on their learning algorithm, allowing robots to move more quicker in difficult surroundings. In general, it eliminates typical human handling errors while keeping a consistent throughput rate.
Whether it’s mixed-SKU pallets or many shipments of the very same SKU, automated robotic depalletizing boosts productivity, lowers operating costs, and fosters a safe working atmosphere. Furthermore, warehouse workers are less likely to suffer from chronic diseases, injuries, and other medical issues. The best part is that your firm may profit from both human cognitive and artificial intelligence.